Custom plastic extrusion designed to your industry needs
Custom plastic extrusion designed to your industry needs
Blog Article
A Comprehensive Guide to the Refine and Advantages of Plastic Extrusion
In the huge world of manufacturing, plastic extrusion emerges as a very efficient and vital process. Altering raw plastic right into continual profiles, it caters to a wide variety of markets with its exceptional flexibility.
Recognizing the Essentials of Plastic Extrusion
While it may appear complicated in the beginning look, the procedure of plastic extrusion is essentially easy - plastic extrusion. It is a high-volume manufacturing method in which raw plastic is thawed and shaped into a continuous profile. The process starts with the feeding of plastic product, in the form of powders, granules, or pellets, right into a warmed barrel. The plastic is then melted making use of a combination of warm and shear, used by a turning screw. When the molten plastic gets to completion of the barrel, it is forced via a tiny opening known as a die, forming it into a preferred type. The shaped plastic is then cooled, solidified, and cut right into wanted sizes, finishing the process.
The Technical Refine of Plastic Extrusion Explained
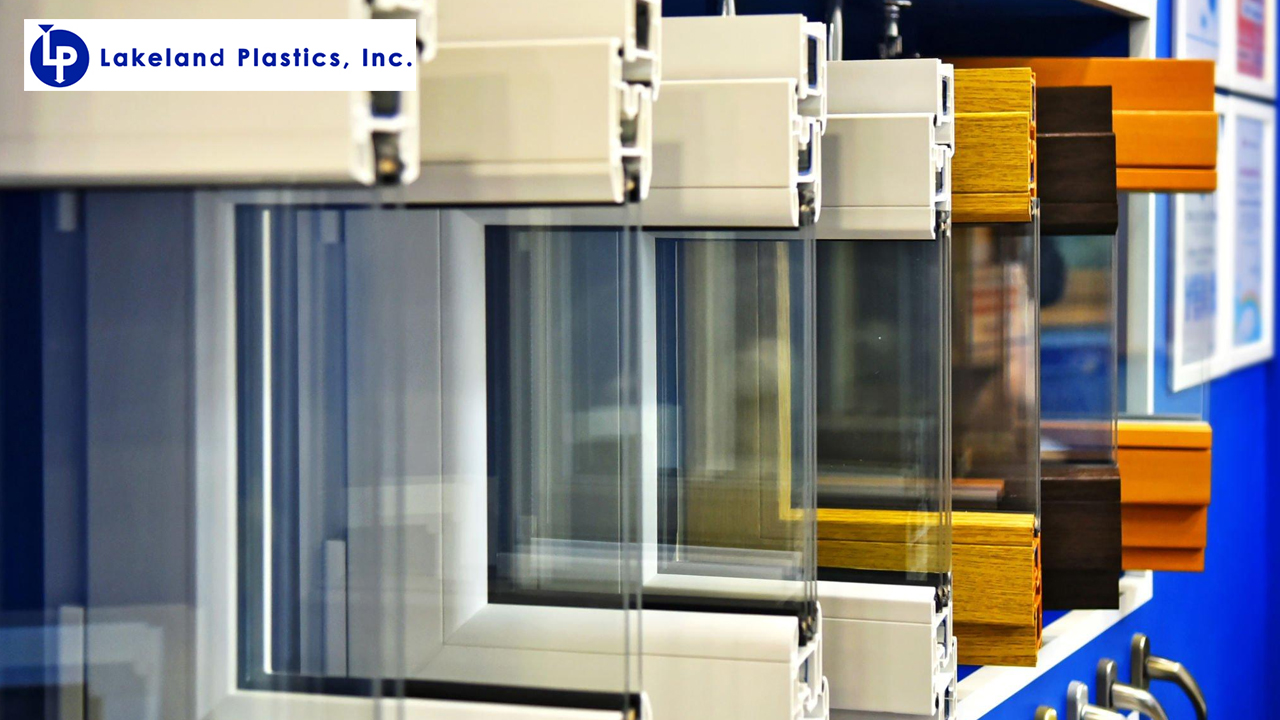
Kinds Of Plastic Suitable for Extrusion
The option of the right type of plastic is an important element of the extrusion process. Numerous plastics use unique residential properties, making them a lot more fit to certain applications. Recognizing these plastic types can significantly boost the extrusion process.
Contrasting Plastic Extrusion to Other Plastic Forming Techniques
Understanding the types of plastic appropriate for extrusion paves the method for a wider conversation on just how plastic extrusion piles up versus other plastic creating methods. Plastic extrusion is unmatched when it comes to creating continual profiles, such as gaskets, pipelines, and seals. It additionally allows for a regular cross-section along the size of the item.
Secret Advantages of Plastic Extrusion in Manufacturing
In the realm of manufacturing, plastic extrusion offers several significant benefits. One noteworthy benefit is the cost-effectiveness of the procedure, that makes it a financially enticing production method. In addition, this strategy provides superior item versatility and boosted manufacturing rate, consequently raising overall production performance.
Cost-efficient Manufacturing Method
Plastic extrusion jumps to the center as a cost-efficient manufacturing technique in manufacturing. This process stands apart for its capacity to create high quantities of product promptly and effectively, providing manufacturers with substantial cost savings. The key expense benefit is the capability to make use of less costly raw products. Extrusion utilizes polycarbonate products, which are less pricey compared to ceramics or steels. Better, the extrusion process itself is reasonably straightforward, decreasing labor costs. Additionally, plastic extrusion needs much less energy than typical manufacturing techniques, adding to reduced functional expenses. The procedure also minimizes waste, as any kind of excess or malfunctioning materials can be recycled and reused, supplying one more layer of cost-effectiveness. Overall, the monetary benefits make plastic extrusion a very attractive choice in the manufacturing market.
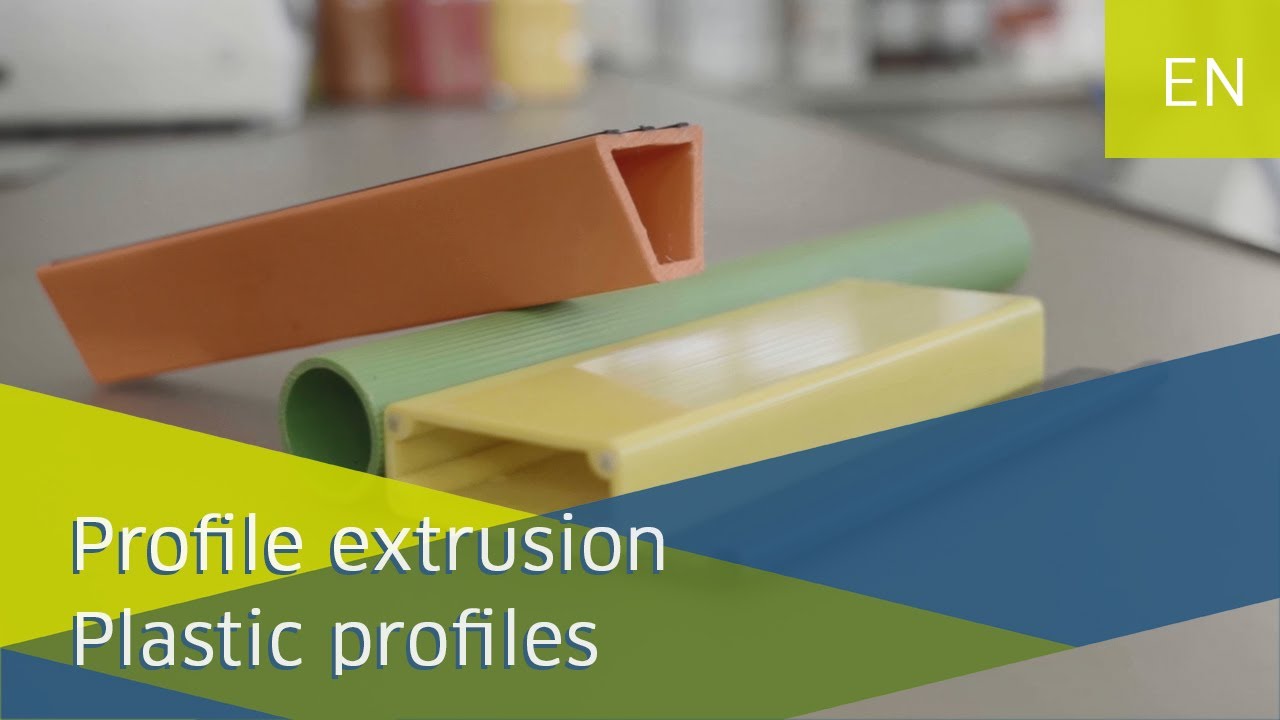
Superior Product Versatility
Past the cost-effectiveness of plastic extrusion, an additional considerable advantage in manufacturing lies in its remarkable item versatility. This process permits for the creation of a wide array of products with differing shapes, sizes, and layouts, click here to find out more from straightforward plastic sheets to elaborate profiles. The adaptability is credited to the extrusion pass away, which can be customized to generate the wanted item design. This makes plastic extrusion an optimal solution for markets that require tailored plastic components, such as auto, construction, and product packaging. The ability to generate diverse items is not just valuable in meeting specific market demands but also in making it possible for producers to discover new item lines with minimal capital financial investment. Essentially, plastic extrusion's item adaptability cultivates advancement while enhancing operational effectiveness.
Enhanced Production Rate
A substantial benefit of plastic extrusion hinges on its improved production rate. This production procedure permits high-volume production in a fairly brief time span. It can generating long, continual plastic profiles, which considerably minimizes the manufacturing time. This high-speed production is specifically beneficial in markets where huge amounts of plastic components are required within limited target dates. Couple of various other production procedures can match the rate of plastic extrusion. Furthermore, the capacity to preserve regular high-speed manufacturing without compromising item high quality sets plastic extrusion aside from other approaches. The improved production speed, consequently, not only makes it possible for makers to satisfy high-demand orders but also adds to increased efficiency and cost-effectiveness. This advantageous feature of plastic extrusion has actually made it a recommended option in numerous industries.
Real-world Applications and Influences of Plastic Extrusion
In the world of production, the strategy of plastic extrusion holds profound importance. The economic advantage of plastic extrusion, largely its cost-efficient and high-volume outcome, has changed production. The market is constantly making every effort for technologies in recyclable and naturally degradable products, suggesting a future where the benefits of plastic extrusion can be preserved without endangering ecological sustainability.
Verdict
Finally, plastic extrusion is a reliable and extremely reliable approach of changing basic materials into diverse items. It supplies many advantages over other plastic creating official source methods, consisting of cost-effectiveness, high result, very little waste, and style versatility. Its effect is profoundly felt in various industries such as construction, automotive, and customer products, making it an essential process in today's production landscape.
Delving deeper right into the technical process of plastic extrusion, it begins with the option of the proper plastic material. When cooled, the plastic is reduced into the called for sizes or wound onto reels if the item is a plastic film or sheet - plastic extrusion. Contrasting Plastic Extrusion to Various Other Plastic Forming Methods
Understanding the kinds of plastic ideal for extrusion leads the method for a broader conversation on just how plastic extrusion piles article source up against various other plastic forming approaches. Couple of other production processes can match the rate of plastic extrusion.
Report this page